Industry Talk
Regular Industry Development Updates, Opinions and Talking Points relating to Manufacturing, the Supply Chain and Logistics.How AI Solves the Riddles of Inventory Management
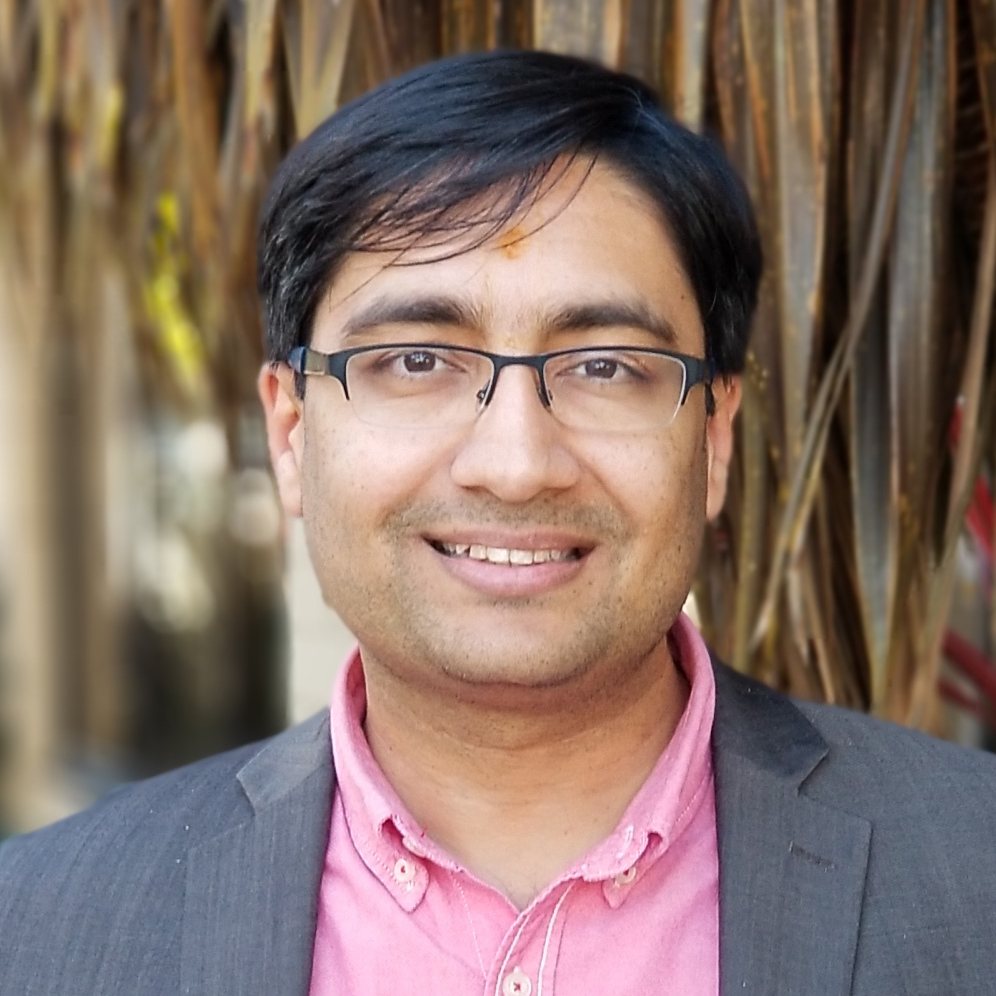
The problems that pervade inventory management are well known: Excess inventory languishes in warehouses, tying up millions of dollars in working capital. Stock shortages cut into margins and hurt brand image. Companies face hefty penalties from buyers if they can’t meet thresholds in service level contracts on time and in full.
The solution, however, has remained elusive — and not for lack of effort or investment. Multinationals employ thousands of planners and spend millions of dollars on an alphabet soup of software to manage inventory and other links in the supply chain, from ERP, MES, MRP, CRM and WMS to planning and logistics tools.
It’s a losing battle. Organizations are confronted by massive quantities of data that multiply by the minute, across every function that affects inventory management — planning, procurement, production, distribution and fulfillment. Contracting with channel partners for some of those processes complicates the challenge.
Those siloed functions make holistic visibility nearly impossible to achieve with standard applications and Excel. When a problem arises, it could take days or weeks to pinpoint the root cause — that one weak link that disrupts a fragile supply chain. Hitting the ideal balance of right product, right place, right time can be more a matter of luck than it is of effective inventory management.
Applying AI Cognition to Inventory Challenges
But what if large organizations in pharmaceuticals, CPG, manufacturing, retail and other industries could apply the power of cognitive automation, artificial intelligence and machine learning to solve the previously unsolvable riddles of inventory management? In fact, they can.
Leaders are seizing the opportunity offered through what’s called cognitive inventory management, referring to the “thinking” capacity of AI to understand the multitude of real-time dynamics that affect inventory levels. Cognitive inventory management is differentiated from traditional tools in its ability to predict scenarios, recommend actions and take actions, either with human approval or autonomously.
For example, AI-powered cognitive inventory management makes recommendations that address such questions as:
- How can we reduce working capital in excess stock?
- What’s the best way to get product from factory to warehouse?
- How can we best manage expiring inventory?
- What’s our optimal minimum and maximum safety buffers?
- Why are we always overstocked at one warehouse?
Presented with those recommendations, managers can accept, reject or revise a recommended action. And once they gain confidence in cognitive inventory management, managers can allow the system to function autonomously, freeing up time from routine tasks to focus on more strategic decision-making.
Cognitive inventory management goes far beyond conventional tools and the limited insights they provide. Based in the cloud, it extends the benefits that organizations have already seen by moving applications into a more accessible cloud environment from siloed on-premise systems.
With enterprise-scale compute capacity, cognitive inventory management is able to crawl in near real-time across diverse systems, processing terabytes of data from billions of transactions. That data is consolidated, normalized and enriched, providing the foundation for AI analytics and the data-driven recommendations that distinguish cognitive inventory management.
AI Breakthroughs for CPG Companies
As an example, consider CPG companies that are facing challenges such as product volatility in a given market. It’s a constant struggle to try to balance inventory against erratic demand, given hundreds of millions of material movements a day and billions of transactions a year.
For such CPG companies, cognitive inventory management harnesses data from disparate systems, including ERP, CRM, MES, WMS, planning, logistics, weather, data lakes, excel sheets, etc. It tracks stock in, stock out and stock remaining, and accounts for such factors as order volatility, demand volatility, production volume, available stock and more.
Utilizing AI, cognitive inventory management can then recommend optimal stock levels for hundreds or thousands of SKUs at any given distribution center. That’s traditionally been the role of human planners, but data volumes and complexity make it virtually impossible for humans to truly optimize inventory management.
Savings can amount to hundreds of millions of dollars as CPG companies avoid tying up working capital, and the high costs of excess inventory consuming valuable warehouse space. CPG companies can also fine-tune production to demand and improve service levels, driving newfound cost-efficiency across the organization.
That’s just one example of the game-changing value that AI delivers with cognitive inventory management. Let’s face it: Hiring more planners and supply chain managers won’t solve the problem. Neither will out-dated legacy software that relies on statistics. AI offers a tremendously exciting opportunity to at last gain full control over inventory.
For companies that are looking to adopt AI, I’ll offer the following points:
Be bold with next-gen tech. Companies with innovative leaders who embrace technologies like AI, IoT and others can make a quantum leap ahead of rivals stuck in the status quo of 1990s-style software and brute-force processes. We’re seeing that first-hand as global organizations begin reaping the rewards of cognitive inventory management.
Don’t wait, the future is now. It’s easy to rationalize putting off an AI project until you upgrade your ERP or deploy a new planning tool. That’s an opportunity lost. The beauty of an AI solution is that it layers atop your existing legacy or cloud systems, with no rip and replace necessary. AI non-invasively complements your infrastructure with groundbreaking capabilities that can forever reshape how you manage inventory.
Take a holistic approach. It’s sound practice to first focus AI on a particular issue, such as balancing stock across distribution centers (DCs), but with a holistic approach that captures data from multiple systems. Since DC stock levels are influenced by dynamics both downstream and upstream of a DC, AI should be applied across all aspects of the supply chain that affect stock levels.
AI-based cognitive automation is still young, but already it’s rewriting the rules of inventory management. In a matter of years, the waste and inefficiency of conventional inventory management will no longer be written off as a cost of doing business. Cognitive inventory management gives planners and supply chain leaders capabilities far beyond what’s been possible in the past.