Warehouse Management
Warehouse Management (WMS) Systems & Software, picking, Third party logistics, Inventory control, TMS, YMS, Cross docking, Virtual Warehouse and Web based WMS for optimal stock control in the warehouse.How Stowga helped fight the warehouse industry’s “Christmas Bulge”
Christmas in the UK is a time for festivities, family and food! Unfortunately for food retailers the nation’s warehousing capacity often reaches close to breaking point, with huge demand for third-party storage over the winter months ahead of the busiest time in retail. Oakland International, a UK supply chain specialist, was faced with the same […]
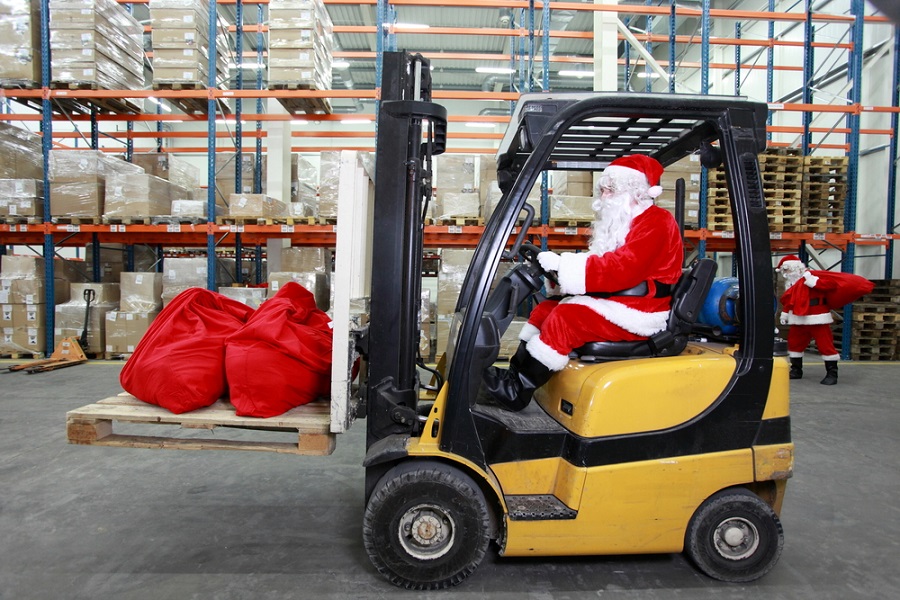
Christmas in the UK is a time for festivities, family and food! Unfortunately for food retailers the nation’s warehousing capacity often reaches close to breaking point, with huge demand for third-party storage over the winter months ahead of the busiest time in retail. Oakland International, a UK supply chain specialist, was faced with the same problem a few months ago – having thousands of pallets of frozen products to store for the months in the run up to Christmas. Working with Stowga they were able to use The Stowga Marketplace to compare hundreds of sites and find the best solution within days – saving both time and money.
THE CHALLENGE
Most products have elements of seasonality and cyclicality, but not many things are as extreme as frozen Christmas food. In the UK we consume over 10 million turkeys over the festive period and the average Brit consumes over 6,000 calories on Christmas Day itself, the peak day of the year for food consumption!
Three things made Oakland’s requirement particularly challenging:
1. Goods needs to be kept frozen: frozen storage is much more difficult to find than ambient.
2. Timing: Christmas is by far the busiest time of the year for the industry.
3. Flexibility: Oakland only wanted the space for a short-period of time so the option of taking a long-term fixed lease on a building was out of the question.
PROCESS
Oakland International needed a way to search all the available options in an efficient way rather than having to call the warehouses they already knew in the area individually. They went into the Stowga Marketplace and specified their requirements using the filters to shortlist sites against: location, timing and temperature control among other things.
This process essentially substituted what could have been weeks – or more likely months of calling and following up with a handful of sites, with a digital process that instantly compared hundreds of suitable sites. The Stowga Marketplace narrowed down the two best options for their requirements, one of which was by far the best choice.
Interestingly, the option they chose was a “grey-space” supplier. Grey space is spare space in an already occupied warehouse, but a warehouse that belongs to a retailer, i.e. a company whose core business is not logistics. Grey space is therefore ‘off-market’ and is not available through traditional agency channels.
What made this even more interesting is that the supplier was ASDA, which is an end customer for many of Oakland International products which saves transport costs and reduces inefficient transport movements since Oakland can now send in chilled products daily and collect frozen stock to replenish own frozen storage at Redditch.
ASDA, as an innovative and forward-thinking company has been working with Stowga to help monetise empty capacity across their warehouse portfolio and make the most of their real estate assets. They had already transacted through the Stowga Marketplace with customers including FTSE-100 companies and had strong positive recommendations through the platform.
Rob Symons, Commercial Operations Manager, from ASDA comments:
“Using the Stowga Platform helps bring opportunities that we would otherwise never see, and it allows us to market our space, on our terms, to make the most of our warehousing assets.”
OUTCOME
Both Oakland and ASDA agreed contracts within a matter of weeks and the space was booked 9 months ahead of when it was needed, removing Oakland’s risk of future supply constraint and giving them flexibility.
Robert Hardy, Commercial Director at Oakland International comments:
“Using Stowga to find spare warehousing capacity over Christmas not only saved us weeks of manual work but also helped us find the best suited warehouse on the market, saving us a significant amount of time and money versus alternatives. Definitely our go-to platform for finding reactive capacity warehousing in the future.”
Oakland was so pleased with the process that they ended up using the ASDA site again, for a second deal, within days of the first one to take more pressure of their supply chain’s seasonal peak. As a company that looks to embrace technology to improve its operations, the benefit more flexible warehousing brings is ultimately to their customers and allows Oakland to provide them with a superior service.
The Stowga Marketplace has already unlocked over a million empty pallet spaces and is the biggest platform for warehousing space and services in the UK. Businesses are increasingly being forced to think about how to optimise their assets and they are looking to embrace many of the Sharing Economy principles we’ve seen in the personal sector, into their operations. Sharing resources on a flexible basis allows both companies to cut costs but also be more nimble and agile with their supply chain. So, this year, share more than presents and food over Christmas… share your space.