Manufacturing/ERP/MRP
Manufacturing Software News, Case-Study Applications, Product Information, Best-Practice and Thought-Leadership ArticlesHow to Streamline Part Design for CNC Machining
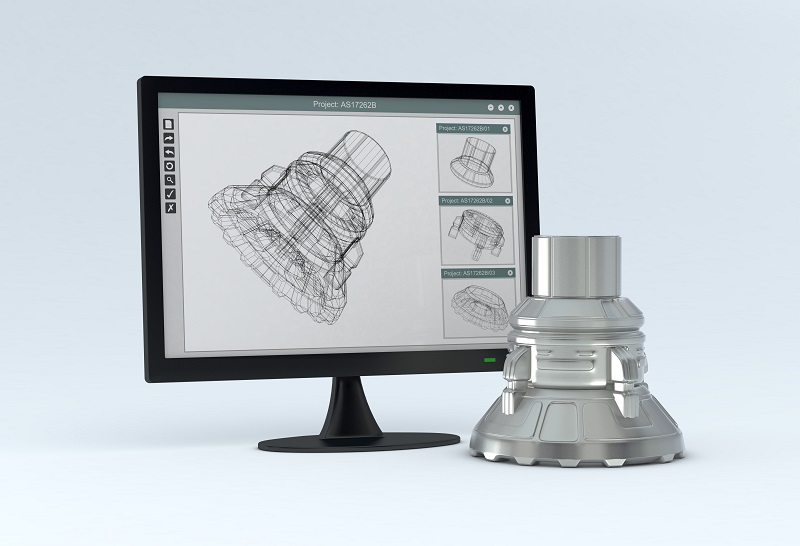
The manufacturing and part designing space have seen a great revolution through CNC technology. While CNC technology has been available for a while, it offers high-quality precision machining, and many more benefits in terms of the production of parts. However, to maximize the use of CNC machining technology, designers must have a grasp and understanding of certain production rules. These rules will help to streamline part designs for CNC machining.
Spending quality time evaluating and improving part design for CNC machining will lower the manufacturing cycle, lower cost, and optimize part quality and efficiency. So, the question is, how do you streamline part design for CNC machining?
Choosing the Right Material
The type of machining materials for CNC machining will influence the cycle times and performance. In choosing the right materials, factors such as load to bearing, durability, overall machining structure, part design, part’s use, and many more physical properties must be considered. This will help you achieve high-quality parts after production. Also, these properties of materials and tooling behavior will influence machining tool factors. These include feed rate, motor power, maximum spindle speed, and spindle motor torque.
Overall, to determine the properties you need, define the function of CNC milled parts, the environment it will work in, and the stress load endurance of the material. This will help you streamline your part design for CNC machining. There are a wide variety of materials for CNC machining; the most common two are metals and plastics.
Metals
In the CNC machining space, Manufacturers use varieties of metals for CNC machined parts. They include aluminum, brass, stainless steel, steel, copper, and many more. Most manufacturers prefer aluminum and other soft metals because of their ease of machining. Furthermore, these CNC materials offer less time to machine, lesser weight, and are generally less expensive. However, they cannot take on much stress compared to hard metals such as carbon steel and stainless steel. Hard metals like steel are of primary consideration where strength is required. The cons of these types of metals are that they weigh more and take much time to machine, which greatly affects the project’s cost.
Plastics
Plastics do not offer the rigidity and strength offered by metals, but they are cost-effective options for your project. Irrespective of this, the use of plastic material depends on the use of the parts. So, it’s important to consider this to streamline your part’s design. While plastic materials are easy to machine at a lower cost, it’s hard to achieve tight tolerances and are more susceptible to warping.
Consider Design Limitations
When it comes to streamlining your part design for CNC machining, it is essential to consider the complexity of your designs. This will help you plan ahead of what type of tools are required for CNC machining operations. Access to CNC machining tools is a great limitation for CNC manufacturing. This is because reaching multiple faces on your workpiece depends on how much a machining tool can easily rotate severally in a short period. If your part design is complex, you need to continuously recalibrate to adjust the machine using a new coordinate system. This, in turn, leads to an increase in the time and cost required to complete a project. There must be easy access to different machining tools like the 3-axis, 4-axis, and 5-axis CNC machining tools to deal with this limitation. Of these types, the 5-axis can handle complex designs easily.
In streamlining your part designs for CNC machining, rotating a workpiece four or fewer than four times or more than four times should not be a problem. With a 5-axis CNC machine, complex part designs can be machined easily. While it is effective for complex design, the tools cannot handle internal geometries. Hence the need for specialized tools for internal geometries. Once these tools are available, you can easily streamline your part design for CNC machining.
Consider Size Limitations
The size of the part design poses a limitation making overall part size an essential consideration when designing it. The size of your part can be limited via machine capabilities available for manufacturing coupled with the depth of cut needed for creating a high-quality piece. Designers must bear these factors in mind, especially if the plan is to use lathe or milling machines.
For milling, size is a great consideration. While a machine can penetrate 38 inches along the y axis, machining a part to that height or level may be hard. This means that the size and feature of the workpiece must be a little less than 38″ to allow for the depth of cut and tool clearance. Hence, your design size is another important factor in streamlining your part design for CNC machining.
Be Meticulous to the Accuracy
To streamline your part’s design for CNC machining, always be meticulous to the accuracy and precision. Maintaining accuracy and precision depends on the following processes and procedures, which must be prioritized:
Working Environment: Your part’s accuracy depends on a working environment that offers stable conditions, including humidity, temperature, pressure, and many more
Equipment Condition: CNC machining requires consistent preventive maintenance to help keep all machining equipment in perfect running condition.
Machine Calibration: Recalibrating CNC machining at regular intervals is a great way to ensure accuracy and precision in manufacturing your parts.
Tool Monitoring: All CNC machining equipment must be monitored as they wear out easily. Then proper maintenance and replacement should be ensured.
Work holding: To achieve accuracy and precision, you must minimize vibration by using proper work holding setups to secure your workpieces for the machining process.
Programming: Ensure the use of skilled manufacturing engineers who understand how to use different tools with different speeds and approaches to effectively produce accurate CNC milled parts.
Machinist Experience: Engineers with more experience in CNC machining are more likely to grasp the subtle nuances that can help ensure accurate part production.
Conclusion
Manufacturing high-end quality parts are dependent on complex combinations of tools and processes, CNC machines, software, and skilled machinists. Considering these factors will help ensure quality and consistent machined parts that offer the right accuracy and precision. To continually manufacture quality parts, you should invest in high-quality CNC machines. This will help you meet the constant demands for accurate productivity, increased complexity, ever-changing parts, and the need for consistent part quality.
Although all this information put together as one might seem a little bit intimidating, note that designing your parts is a whole process. As much as you keep these information guidelines in mind when streamlining your part’s design, you are on the right path to creating your state-of-the-art product.