Industry Talk
Regular Industry Development Updates, Opinions and Talking Points relating to Manufacturing, the Supply Chain and Logistics.Manufacturers are on the verge of a digital transformation journey, but where to start?
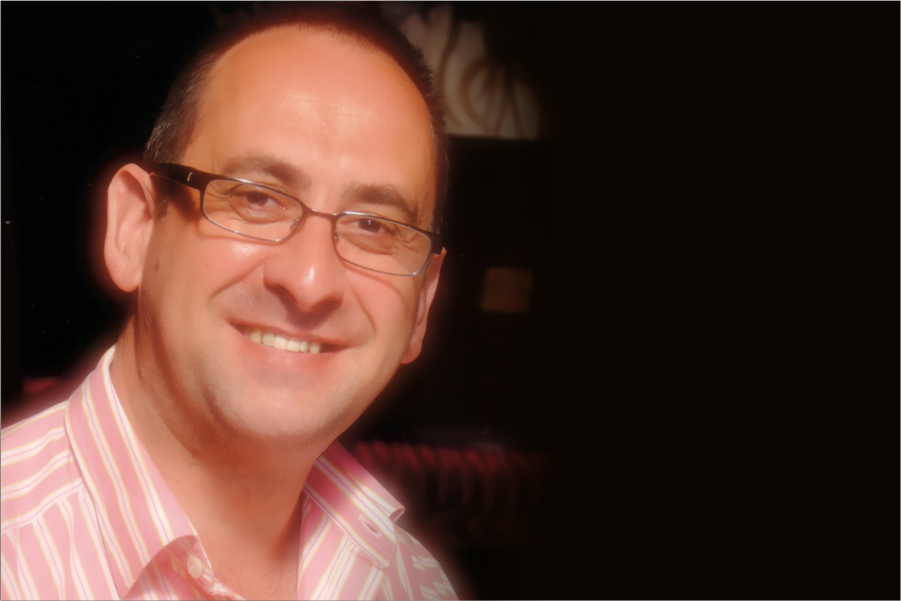
The manufacturing shop-floor is where the real action happens – the area where production is carried out. For most manufacturers, and by their very definition, that will also be the most critical area of their business operations and often the one that consumes the most cost in labour, material and machines. Despite that and even in 2018, many manufacturers are still reliant on using outdated, laborious and error-prone manual processes, such as pen and paper to record critical data. In the current era – where digital capability is essential, manufacturers can no longer rely on these archaic methods if they are to compete in their increasingly tough markets. This applies to manufacturers with a single production facility servicing a niche market all the way to those with larger facilities or multiple facilities on a global scale. Especially, when looking at the evolving nature of the manufacturing sector, it becomes even more imperative that organisations equip their teams with the right tools. However, in reality, many firms are struggling to embrace the latest technological innovations.
This is evident in our recent research – surveyed over a hundred manufacturers – to reveal that only six per cent of manufacturers consider the level of their IT capabilities to be at an optimal level, with 64 per cent rating it as just ‘average, weak or non-existent’. This reinforces the notion that production is being held back by a lack of robust IT capabilities at shop-floor level, despite the industry being on the cusp of the fourth industrial revolution. Nevertheless, the survey results inform us that manufacturers are well aware of these shortcomings when it comes to shop-floor capabilities but aren’t tackling the issue head-on. So why are they not taking the bull by its horns?
One of the key issues is that many manufacturers don’t have a full understanding of what digital transformation really is. There is a broadly accepted theory that digital transformation is either some gigantic and expensive undertaking that will consume their entire budget or is a marketing fantasy fuelled by the technology sector (remember the dot-com era?). Yet neither is true. Firstly, digital transformation projects can start very modestly and be focused on precise process areas, before being expanded out when confidence and evidence of benefit is realised. Secondly, it is not a failure to invest in digital transformation itself that will be damaging to manufacturers, it will be the failure to reap the much-needed tangible business benefits that digital transformation can provide that will prove costly.
Another factor which contributes to this misconception is that digital transformation is a very broad term which covers a very wide spectrum of technologies and techniques. Those not yet convinced of the role of artificial intelligence, machine learning and robotics, for example, may dismiss the whole digitalisation opportunity. This is akin to the old idiomatic expression of “Don’t throw the baby out with the bathwater”. In the short to medium term, most manufacturers will gain significant benefit by investing in proven automated data collection technologies, real-time manufacturing and quality analytics and statistical process control solutions to replace those predominantly manual data collection processes. That is digital transformation, right there!
The impact of digital transformation is not just an external one. The perspective of highly-skilled digital natives looking to enter the industry, those moribund manufacturing environments are simply not going to be attractive workplaces for young professionals entering the workforce. This will cause talent to leech out to other more progressive manufacturers, and once this happens, reversal becomes ever more challenging and risks putting the manufacturer into a slow decline.
Unfortunately, those that are ready and willing to embark on a journey of digital transformation, often do not know where to start.
As with every journey, regardless of the direction, length or difficulty – each begins with the first step. The most important thing that manufacturers can do on a digital transformation journey is to make that first step. This may be beginning with a learning and discovery phase. It may also include creating a coherent business case; gaining executive sponsorship; putting the right skills and talent in place or to think about training and education requirements; developing a short-term plan as well as a long-term strategy and roadmap; or by identifying a potential list of technology solutions or industrial IT service providers. What that first step is, or needs to be, will vary from business to business, but the most important point is to create a plan and take the first step.
Over the last decade or two, the changes on the manufacturing sector brought about by technology, media, distribution, consumer trends and global economies have been intense, and that pressure will continue to grow – exponentially. Manufacturers must therefore optimise their operations across the three core dimensions efficiency (cost), quality (value) and uncertainty (risk). In my view, this means digitalisation is a necessity and not an option for manufacturers. The quicker that is realised and the quicker those first steps are taken, the better for them.