Industry Talk
Regular Industry Development Updates, Opinions and Talking Points relating to Manufacturing, the Supply Chain and Logistics.Solving the Lost Trolley Problem: How Ports Are Quietly Getting Smarter with IoT
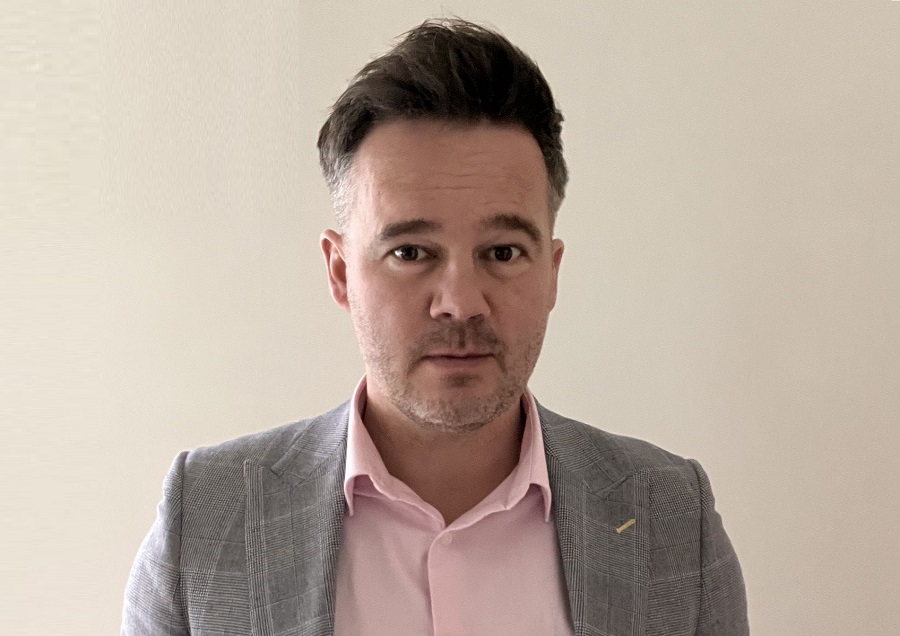
There’s no shortage of big projects and ideas in the world of ports and logistics, including smart terminals, automated cranes and green shipping corridors, such as those seen at the Port of Rotterdam. But often, the real operational headaches aren’t about grand strategy. They’re about the small things that quietly go wrong every day. Like the missing luggage trolley that forces a passenger to drag a heavy suitcase across a terminal. Or the staff members who end up searching for trolleys when they should be doing other work.
These aren’t dramatic failures, but they chip away at efficiency and customer experience. And they happen more often than many people realise. For years, the assumption has been that this kind of problem comes with the territory. But that’s starting to change, thanks to advances in IoT-enabled tracking devices and low-power connectivity that are making it much easier and cheaper to keep track of mobile assets like trolleys in ports. Gareth Mitchell, UK Partner Manager, Heliot Europe, explains.
The Real Cost of Misplaced Trolleys
If you spend any time in a cruise terminal or ferry port, it quickly becomes obvious how dependent the whole experience is on the availability of trolleys. Passengers use them to move bags, customs officers rely on them for throughput, and operations teams are constantly rotating them from one end of the terminal to another to keep things moving smoothly. When the system works, nobody notices. But when a batch of trolleys disappears, or simply ends up in the wrong place, it creates a domino effect that can have significant consequences.
For example, when it becomes apparent that a fleet of trolleys have gone missing, someone has to stop what they’re doing to go find them. Port staff may get pulled from more important tasks to investigate, only to find that they have since sailed to another country, mistakenly being taken on board by other port staff before setting off. Passengers are left waiting too. And because nobody is quite sure where the missing trolleys went, the solution often ends up being ‘just order more’.
This quickly becomes expensive. A single trolley typically costs between £200 and £500. Many ports manage fleets of several hundred or even thousands of trolleys. Losing 10% of a fleet in a year could mean replacing 50 to 100 trolleys, costing anywhere from £10,000 to £50,000 annually. Over 10 years, this could add up to half a million pounds or more, on replacements alone. And that’s before factoring in the hidden costs: staff time spent searching, the knock-on delays to operations, and the frustration felt by both employees and passengers. And from a passenger’s perspective, arriving to find no trolleys available can be a frustrating first impression, especially after a long journey or with heavy bags in hand.
Without knowing where trolleys are at any given moment, these issues tend to repeat week after week. Add in the prospect of contractual penalties, whether formal loss charges or demurrage-style fees for mismanaged equipment, and the problem grows from a simple nuisance into a recurring financial liability. This financial and operational drain makes the case for tracking technology clear. With affordable IoT devices now available, ports can gain visibility on their trolley fleets, reduce losses, and improve overall efficiency.
Why Tracking Is Now a Feasible Option
Until recently, tracking trolleys didn’t seem like a realistic idea. The technology existed, but it was expensive, power-hungry, and mostly aimed at high-value goods. Sticking a GPS tracker on every asset felt like overkill. But that’s no longer the case. And the smart port market itself is growing, and expected to reach $7.12 billion by 2027, showing clear demand for these types of improvements in the industry.
Over the past few years, there’s been a quiet revolution in IoT tracking. Small, battery-efficient devices are now able to report their location a few times a day, using a combination of connectivity options including Sigfox and other Low-Power Wide Area Network (LPWAN) options, Bluetooth Low Energy (BLE) and WiFi sniffing that don’t require much power to transmit. That means you can get months or even years of useful data without constant maintenance or expensive infrastructure. The batteries on these devices typically last around 5 years without maintenance.
You don’t necessarily need pinpoint accuracy all the time either. For trolley tracking, it’s not about following every movement in real time. What matters is knowing where they generally are, whether they’ve left the site or a particular geo-fenced area, and if they’re ending up in unexpected places. That level of insight is enough to solve most of the headaches ports are facing around trolley loss and availability. However, if a “black hole” of vanishing trolleys is identified, operators can still selectively drill down and trace the journey in more detail when needed.
The technology is now so mature that it’s being used not only in ports, but across retail, logistics, and warehousing too, or essentially anywhere that mobile assets have a tendency to go missing. What’s changed is that the economics have finally caught up with the need, making this a viable option for those working in ports where trolleys are a key and valuable part of their operations.
From Visibility to Action
Of course, knowing where your trolleys are is only part of the story. The real value comes from what that visibility allows you to do.
For one, it helps avoid the endless finger-pointing that happens when assets are shared between different stakeholders, such as terminal operators, shipping lines, and ground handlers. With location data, you can see who last used a group of trolleys, where they were dropped off, and whether they were picked up again. It creates a shared reference point that makes collaboration easier and more productive.
More than that, it allows operators to spot patterns too. Maybe trolleys always go missing after a certain shift, or they’re being left in car parks outside the terminal. Maybe there’s a breakdown in how they’re being collected and returned between specific cruise calls. These aren’t things you can easily solve without data, but once the data’s there, they’re often straightforward to fix.
It also opens the door to doing more with less. If you know how trolleys are being used, you can reduce over-ordering trolleys, rebalance stock across the terminal more effectively, and give staff a clear picture of what’s needed at specific times. That means better service for passengers, less stress for ground teams, and fewer surprises for everyone involved.
Conclusion
Every port is looking for ways to be smarter, more efficient, and more customer-friendly. And while the spotlight tends to fall on large-scale innovations, sometimes it’s the quieter, more mundane problems that offer the best opportunities for improvement.
Trolley tracking perhaps isn’t as obvious as these large investment projects. But it’s exactly the kind of problem that’s been hiding in plain sight for years. The technology to fix it is here now, and it doesn’t require a big rollout or expensive overhaul. It takes a willingness to look closely at how the small, everyday parts of port operations work, and to start making them better.
In the end, solving the trolley problem is really about building a culture of visibility and responsiveness. And once that starts to take hold, the benefits ripple outward, to staff, to passengers, and to the port as a whole. For ports looking to make smarter decisions without major disruption, investing in trolley tracking could be the simplest, most effective win they haven’t yet considered.