Warehouse Management
Warehouse Management (WMS) Systems & Software, picking, Third party logistics, Inventory control, TMS, YMS, Cross docking, Virtual Warehouse and Web based WMS for optimal stock control in the warehouse.Sprayground pack up their troubles with Fullers Logistics
Slough, Berkshire: 11th September, 2018 – Fullers Logistics, a specialist multi-channel fulfilment and distribution services provider based in the south of England, has announced today that it is providing multi-channel fulfilment and warehouse services to rebel backpack company, Sprayground. Sprayground has evolved into a high quality, global brand with excellent brand awareness, very dedicated fans and […]
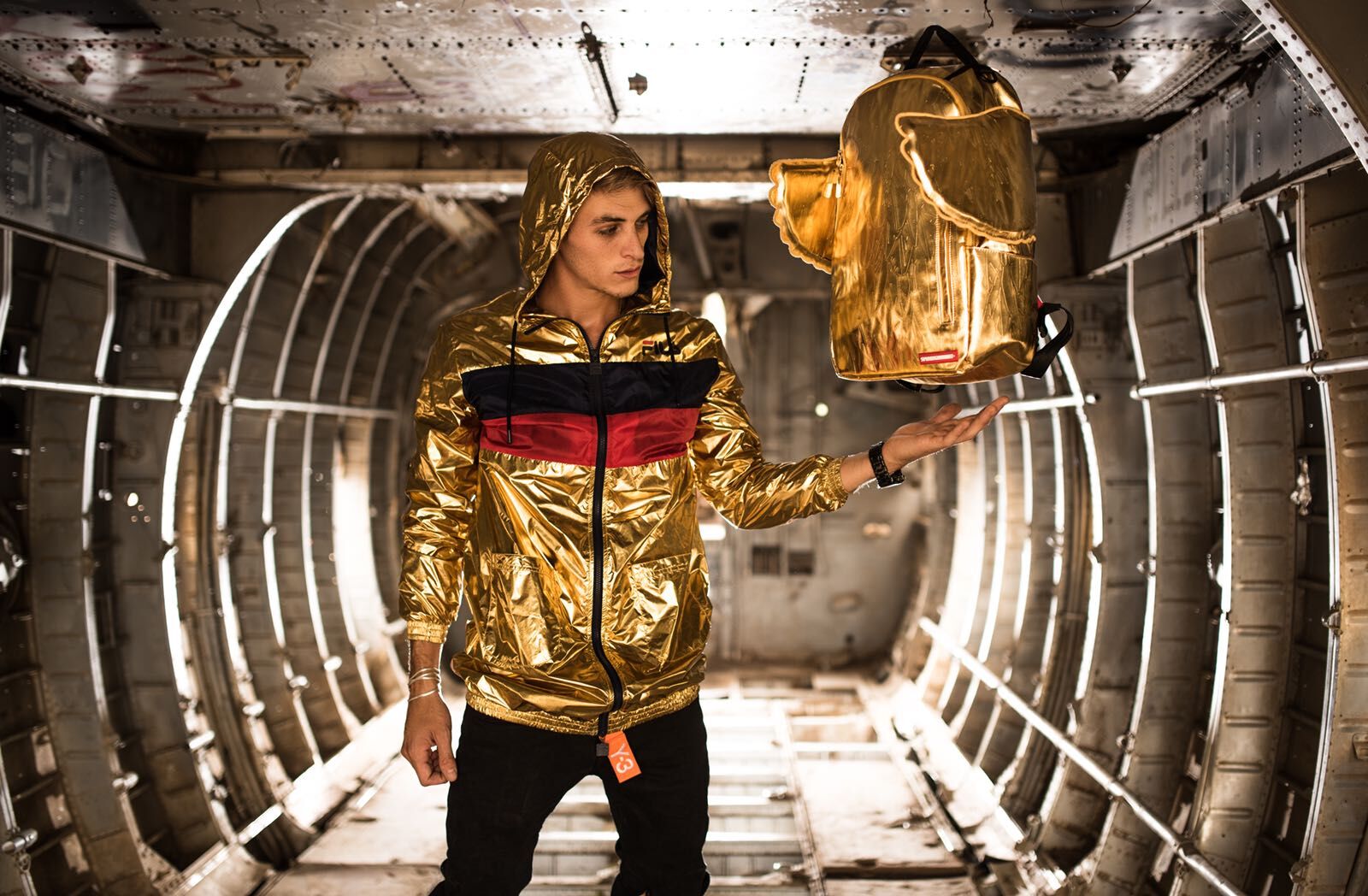
Slough, Berkshire: 11th September, 2018 – Fullers Logistics, a specialist multi-channel fulfilment and distribution services provider based in the south of England, has announced today that it is providing multi-channel fulfilment and warehouse services to rebel backpack company, Sprayground.
Sprayground has evolved into a high quality, global brand with excellent brand awareness, very dedicated fans and repeat customers, many of whom are collectors. Imported from the USA, the backpacks offer unique custom designs in limited edition quantities. In addition to being sold through the company’s incredibly busy e-commerce website, the brand is also stocked at a shop in Box Park, Shoreditch and is distributed to wholesalers and via events around the UK.
Julie Butler, Director at Sprayground explains, “With a premium brand that strives to keep pushing the envelope of creativity, we needed to find a logistics partner that would be able to seamlessly deal with pick, pack and fulfilment across the multiple channels of our business, so we could focus on customer service and product innovation – that’s when we found Fullers.”
Being a small business in the UK market, Sprayground wanted to find a partner that were interested in what they did and had the capability to and understand their challenges.
“Our previous provider was not in a position to meet our growing demands, and when we came across a problem with a delivery, which was becoming a more frequent occurrence, the process to get this rectified could take a long time which was detrimental to our level of customer service we are able to provide,” Butler explains.
“Also, when looking for a new supplier we felt that some of the large logistics companies would not be able to offer us the level of partnership we desired, and some would only stock our products in a northern location. It was vital for us to have easy access to our stock and ideally wanted it near London, close to our shop in case we needed to replenish stock at short notice.”
Fullers recommended using one of its multi-user warehouse sites in Bordon and configured the space to meet Sprayground’s needs. The multi-user option also provides a flexible storage solution for Sprayground, so they can easily scale when there are spikes in demand and extend the space as the brand grows its presence in the UK.
As orders are received via the ecommerce site, products are picked, packed and distributed to the customer via courier. Volume orders placed by the brand’s high street shop or wholesale providers are also picked, packed and shipped from the Fullers warehouse.
A sophisticated and automated warehouse management system provides Sprayground with 24/7 access to reports about stock movement & availability, enabling improved visibility and management across their sales channels.
“As part of our service we proactively review all aspects of the operations we undertake for clients to identify areas where we can improve productivity, increase efficiency and uncover cost savings,” comments Tony Dempsey, Managing Director at Fullers Logistics. “The warehouse management system provides the right level of automation so that Sprayground no longer have to check every order that comes in and the system has significantly decreased the time spent following up with customer delivers or complaints which rarely occur now that the pick, pack and despatch process is a seamless operation.”
Butler concludes, “Fullers provide an efficient service and have a wealth of experience that offers our business excellent value, peace of mind, and they take full responsibility for the whole pick and pack process with no excuses. Our team at Fullers work productively and transparently and are always willing to explore new processes that are tailored to the specific requirements of our brand.”