Industry Talk
Regular Industry Development Updates, Opinions and Talking Points relating to Manufacturing, the Supply Chain and Logistics.The shift towards supply chain transparency with asset traceability for manufacturers
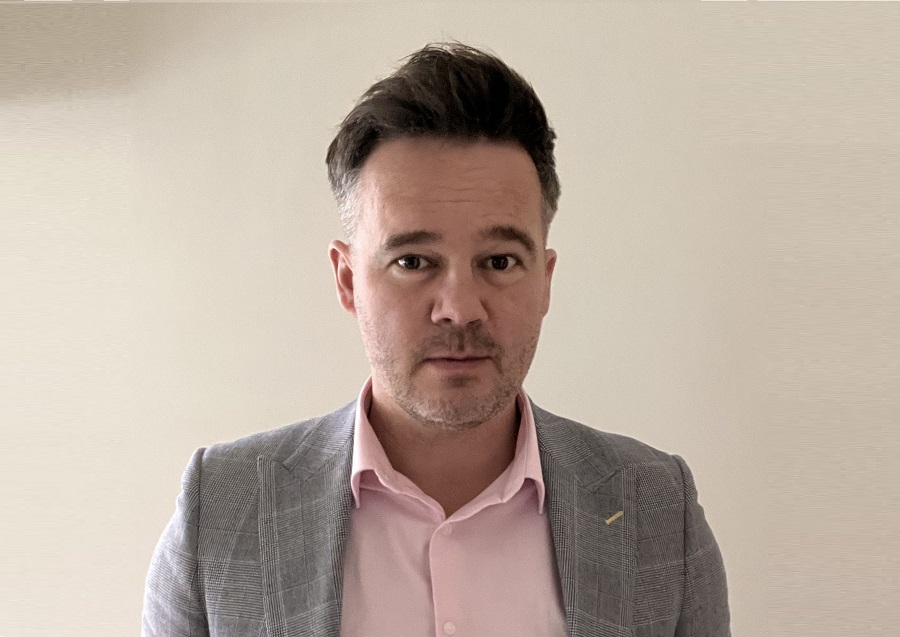
Over the last few years manufacturers and their supply chains have come up against an array of challenges. There was the COVID-19 pandemic between 2020 and 2023; the Suez Canal obstruction in March 2021; the Russian Invasion of Ukraine in February 2022, and ongoing war; and now, in the midst of a global cost of living crisis, there are shipping challenges affecting the transport of goods through the Red Sea, causing further delays and spikes in costs. Collectively, these kinds of events cause supply chain issues for many manufacturers, their customers and consumers to deal with – and they often result in many manufacturers reviewing how they can produce and deliver products more cost effectively to customers.
For many manufacturers, an industry wide answer is to deliver more supply chain transparency and traceability to mitigate against these disruptive moments that can occur. Glass manufacturers, for instance, and their supporting supply chain and logistics partners are not immune to these problems as they manufacture and deliver goods. This is because after glass is produced, A Frame Stillages (trolleys or racks) are often used to transport delicate glass sheets to customers. This often includes deliveries globally and regionally to flat glass processors, construction companies, automotive firms and OEM locations, along with supply chain intermediaries. Within this delivery process, an area that is ripe for improvements surrounds that of improving the upkeep, use and traceability of trolleys that carry glass.
Gareth Mitchell discusses the challenges that glass manufacturers come up against when using A Frame Stillages to transport glass to customers, and explains how a more efficient approach to managing ‘A Frames’ can improve supply chains…
Re-use, optimise and improve
A typical glass trolley costs around £2000. Often the majority of deliveries take place between a flat glass manufacturing plant (or warehouse) and larger customers’ sites. Anecdotally, as deliveries take place, up to 15% of transport racks are lost each year. Therefore, if manufacturers are reviewing areas that they can improve, in order to cut costs long-term, it is worth considering how to take better care of A Frame Stillages. As many of these racks are re-used and recycled for delivery it is important to look after them and retrieve them.
This is even more vital today when you consider that energy costs are increasing during glass production, causing profit margins to become reduced. Additionally, market research tells us that the cost of these racks has generally increased by more than 100% in the last 12 months, and the supply of new racks is proving to be a challenge for some organisations due to a restrictive metal supply situation.
It’s not just about holding onto and reusing racks or replacing lost ones either. It’s about optimising and improving the utilisation of existing trolleys too. For instance, in glass manufacturing, if there is an absence of racks to transport the finished product, often production is halted. Consequently, many manufacturers and supply chain operations are reviewing what they can do better when it comes to using, storing and managing A Frames for deliveries. Many are also asking: how can I locate and collect empty trolleys efficiently or find ones that have been lost? How can I ensure I have enough trolleys for my production line? Additionally, to solve this, some firms might overstock on the number of racks that they have in circulation. This whole process can be better managed with automation – for instance, can operations be digitised automated with more effective inventory management? Is there a better way to reduce friction when “tracking and tracing” and chasing lost trolleys? How can greater proof of delivery be demonstrated in order to improve customer service?
Digitisation equals transparency
Digitisation and the Internet of Things (IoT) is capable of providing the asset tracking capabilities that manufacturers need to improve supply chain transparency and traceability. A Frame Stillages can be easily retro-fitted with tracking sensors that collect their location and movement data. They use GPS and WiFi geolocation to achieve this, that has been designed to be suitable for indoor and outdoor tracking. They are robust too, as they need to function within a manufacturing and industrial environment; and have a battery life of up to five years.
Tracking and recording asset data is no good though if that data cannot be transmitted and shared with operational and management teams to review and draw insights from. How are they to gain a deeper understanding of what racks are being used to support the delivery of glass to customers? Are they able to determine how long racks are stationary, when they are moving, and where they are moving towards? Supporting cloud-based software platforms can feed into manufacturing, supply chain and logistics management systems, and together they can help manufacturers optimise the use of their racks. What is more, they can also help create better relationships with customers and support proof of delivery scenarios. Furthermore, in some situations, misuse of racks can also be tracked, detected and prevented.
For these technologies to function and provide the cost savings that manufacturers hope to achieve, though, they require reliable internet / data connectivity. While the devices used can access a range of connectivity features – such as WiFi or Bluetooth – they predominantly rely on the Sigfox network which is available across many European countries. The frequency that this ubiquitous network operates at is 868 MHz. This allows signals to cover distances up to around 30 miles. Moreover, the radio signals are capable of penetrating materials like concrete ceilings and steel, making them effective in challenging industrial environments.
Achieving a $1m net gain over five years
Glass manufacturers that have adopted this approach to trolley asset tracking are seeing quantifiable benefits too. Their racks and processes become more visible to the entire organisation and more meaningful KPIs can be developed operationally. Theft, delivery losses and replacement costs for racks and glass are minimised, reducing shrinkage.
There are more racks available as data from the trackers helps to optimise circulation times, encourage a faster return of empty racks and more efficient planning within the wider manufacturing process. Furthermore, handling costs and this entire process can be automated too. Data from trackers can be used to reduce manual administration and paper work to record information about glass and the delivery thereof. But also, time spent just searching for racks and glass can be reduced as their location and status can be seen on maps.
Across the board, anecdotally, it is estimated that within a manufacturing scenario, where 1000 trolleys are in circulation, tracking devices can increase the use of existing racks by 10%; the loss of racks can be reduced by 50%; repair costs can be reduced by 25%; and a 25% reduction in handling can be achieved by automating associated labour processes. This equates to a $1 million net gain over five years for many manufacturers. It just makes sense to track trolleys.
Conclusion
In the face of formidable challenges like global crises, geopolitical events, and a cost-of-living crisis, manufacturers are grappling with the need for more resilient supply chains. The inefficiencies surrounding the transportation of delicate goods, like glass, through A Frame Stillages, further compounds these challenges. To navigate this terrain, the call for supply chain transparency and traceability becomes paramount. Digitisation and IoT offer a transformative solution, enabling real-time asset tracking and data-driven insights. By retrofitting A Frame Stillages with tracking sensors and the right kind of data connectivity, manufacturers not only enhance transparency; they achieve substantial cost savings, reduced losses, and improved operational efficiency, heralding a future where digital innovations redefine supply chain resilience.