Manufacturing/ERP/MRP
Manufacturing Software News, Case-Study Applications, Product Information, Best-Practice and Thought-Leadership ArticlesGoing green with obsolete equipment
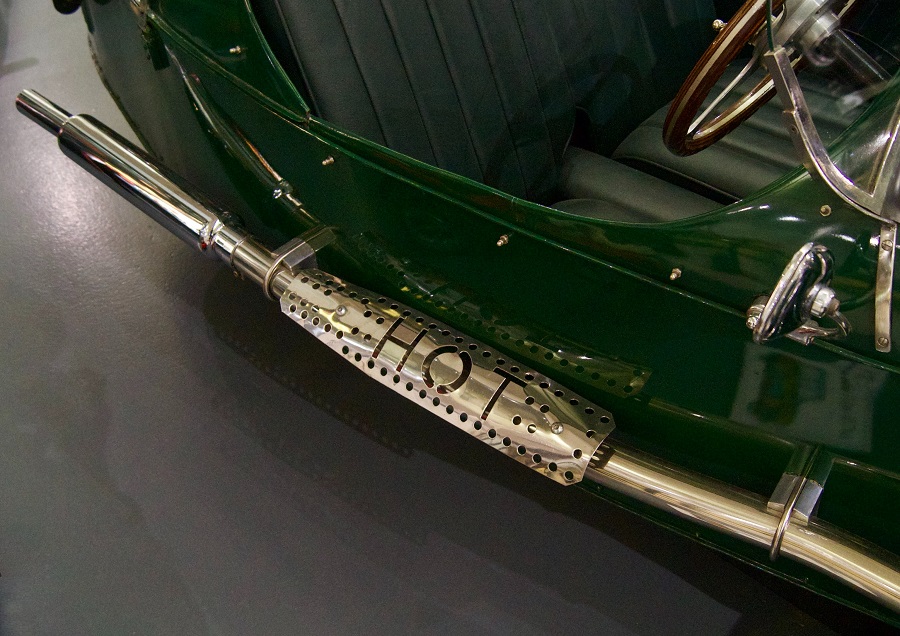
Upgrading to the latest mobile phone or laptop offers the chance to get rid of the old and embrace the new, often in spite of your older model still working. In industrial settings, there’s often a similar pressure to upgrade, chasing higher productivity and efficiency.
However, just because something is old, even obsolete, it doesn’t mean you have to find a replacement. Look around you. Chances are you’re surrounded by manufactured products — from the chair you’re sat on, to the device you’re reading this on.
Every manufactured object started its life as a raw material. This could be a tree, for wooden objects, or mined ores, quarried stones and extracted oils found deep underground.
Every step a product takes along its manufacturing line has some impact on the environment and related ecologies, but resource extraction alone contributes up to half of all carbon emitted into the atmosphere worldwide. Here Neil Ballinger, Head of EMEA at industrial automation supplier, EU Automation (pictured left), discusses how obsolete parts remaining in use can reduce your carbon footprint and have other positive impacts on the environment.
Taking advantage of sunk cost
Despite the impact that resource extraction has on the environment, it continues to take place. Just like any other business, however, extraction companies are simply producing to meet demand. From a manufacturing, repair or maintenance perspective — standing a few steps removed from the point of extraction — the best way to reduce environmental impact and increase sustainability is to assess whether a system really needs upgrading, just because one part has broken, or become obsolete.
A part may become obsolete for a variety of reasons, such as new specifications or regulations, changes in design for varieties of reasons, or simply because the original equipment manufacturer (OEM) has stopped production. However, there are usually still huge amounts of such parts in circulation, and a reliable automation parts supplier will make it simple for you to locate them.
Assessing whether these obsolete parts are workable in a system represents a two-pronged attack on potentially wasteful practices. Primarily, if an obsolete part can be used instead, the demand for the new part is lowered, and secondarily, employing obsolete parts wherever practical makes the most of the resources, energy and associated carbon emitted in the original production of that part.
Just like with new parts, each stockpiled obsolete part passed through the same environmentally damaging pipeline, just to find themselves gathering dust in a warehouse. From there, the best outcome is that they are scrapped and recycled, possibly straight into new parts to be stockpiled indefinitely.
This is unless they’re used. When faced with a part breakdown or end-of-life notice for a vital component, businesses can choose potentially expensive upgrades to the new models and systems, with the prospect of repeating this process when the next end-of-life notice comes along.
Or, they can choose to approach EU Automation, and find the still-working obsolete part that will keep their production line running, save your budget, and help save the planet at the same time.